The Bohning Nock Development Process: Not all nocks are created equal
Date Posted:1 May 2018
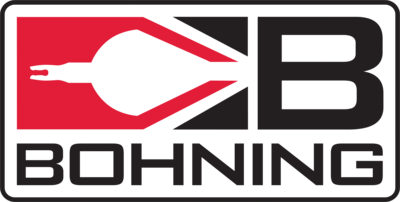

Today's bows are becoming increasingly efficient. A higher percentage of the energy stored in a bow's limbs is transferred to the arrow than ever before. The potential energy stored in your bow is transferred to the arrow via a single component: your nock. The question is, has your nock kept up with bow technology? Bohning Archery has dedicated significant time in testing and research into developing nocks that will withstand the rigors of shooting both today's and tomorrow's high-energy bows.
Every nock designed at Bohning has to go through an extensive series of tests and refinements before it ever hits the store shelves. Special care is taken early in the design phase to ensure each nock is as strong and resilient as possible. Before design is cut into steel, computer simulations are run to find any potential weak points in the nock's geometry. Only after multiple tests and refinements is an injection molding tool built. This is done in-house. Bohning's expert team of engineers and machinists have more than 112 years of combined experience! This vast body of knowledge, skill, and experience is how Bohning nocks are set apart from the competition. Producing multiple identical nocks per machine cycle; each having the same exact dimensional, material, and strength properties as the next is proof of highly skilled craftsmen.
But what does this mean for Bohning customers? Every Bohning nock is molded to incredibly tight tolerances and subject to meticulous standards of workmanship and quality. This translates to superior consistency at a fraction of the cost. And that is just the beginning.
Once production-ready nocks have been run, they are not ready for the shelves until they have passed an exhaustive battery of testing, both in the lab and on the range. Using state-of-the-art destructive testing methods, Bohning nocks are bent, crushed and abused to expose possible design flaws or material defects.
On the range, Bohning's final and most rigorous test is performed: Accelerated life-cycle testing. Using a custom-built bow capable of shooting arrows at kinetic engery levels exceeding 110 ft-lbs (nearly twice that of most hunting bows), Bohning staff put their nock designs through the qauntlet. No design is approved until a signle nock can reliably withstand over 1000 shots* under these conditions without any sign of wear.
Kinetic Energy
So, why focus on kinetic energy (KE)? The answer is simple: KE is the best factor we have for quantifying an arrow's stopping power down range. It is also an excellent way of measuring a bowstring's effect on a nock during the shot. A nock's ability to withstand repeated use under demanding conditions is a testament to its resilience. In engineering terms, "resilience" is the capacity of a material to transmit kinetic energy without permanent deformation. By testing our nocks at extreme levels of kinetic energy rather than just extreme speeds alone, we ensure our nocks are the most resilient on the market.
In archery, mental focus is just as important as all of the practice and careful preperation of your equipment - you shouldn't have to question the reliability of your nock. Only Bohning nocks take the guesswork out of the equation for you.
Information above is provided by Bohning Archery.